Sustainability
Utilizing ChemCycling® to Convert Plastic Waste into Raw Materials
By using postconsumer plastic waste or end-of-life tires as a feedstock for the manufacture of our raw materials for more sustainable coatings, adhesives, and construction and fiber-bonding materials, we can allocate recycling-based feedstocks to our products without sacrificing performance.
Benefits of ChemCycling®
- Replace virgin fossil resources at the beginning of BASF’s value chain
- Third-party certified process (RedCert2 or ISCC Plus)
- Drop-in solution, no reformulation required
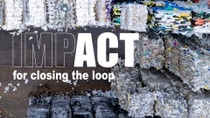
To explore this solution, please get in touch with your BASF account manager.
Recycling plastics
The chemical recycling of plastics is a focal point of BASF’s recycling activities. This technology complements mechanical recycling and can help reduce the amount of plastic waste disposed of in landfill or thermally recovered. Chemical recycling breaks plastics down into their building blocks or converts them into basic chemicals.
Using the pyrolysis process
In our ChemCycling® project, our technology partners use the pyrolysis process to produce pyrolysis oil from mixed plastic waste or used tires that cannot be recycled mechanically. We feed the pyrolysis oil into the BASF Verbund as a substitute for fossil raw materials and manufacture new products for coatings, adhesives, and construction and fiber-bonding materials from it using the mass-balance principle. Our customers can then process the mass-balance products as a drop-in solution, just like conventional products.
Discover
Results: 1
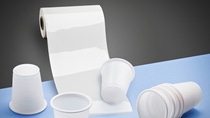
BASF showcases solutions for the entire packaging life cycle at interpack 2020
Discover more sustainable solutions
Go to industries
Contact us
Not found what you were looking for? Reach out to us for assistance.
Subscribe to our News-Service
Don’t miss the latest news on web seminars, sustainability, regulatory and product innovations.