MyIndustryWorld
Acrodur® for natural fibers in Automotive
Acrodur® transforms natural fibers into light and stable composites
Acrodur® stands for
- Water-based binder; no added formaldehyde; low in VOC
- Suitable for a wide range of natural fibers, such as hemp, kenaf, Wood
- Enabling light-weight Solutions
- Possessing superior thermo-mechanical stability
- Applicable for thermoset and thermoplastic processes
From natural fiber to molded composite
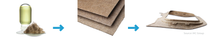
Impregnation of natural fibers with Acrodur® binder
Natural fiber prepregs
Molded composite parts (roof frame)
Natural Fiber – Acrodur®
Sustainable Composites for the Automotive Industry
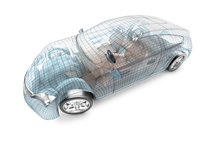
DOOR TRIM
Acrodur®
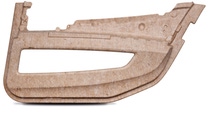
PACKAGE TRAY
Acrodur®
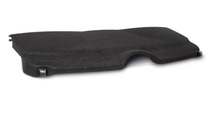
Acrodur®
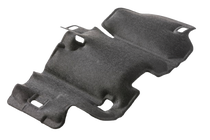
ROOF FRAME
Acrodur®
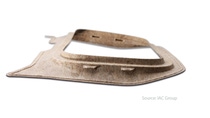
Reducing CO2 emissions without compromising on performance
Resource efficiency and eco-friendliness are becoming decisive factors in the automotive industry nowadays as well. Acrodur® enables you to fulfill more stringent CO2 emission limits without compromising on performance criteria.
Two examples for car interiors and exteriors where natural fiber Acrodur® solutions can support the automotive industry in becoming more sustainable:
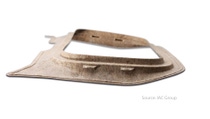
Roof Frame
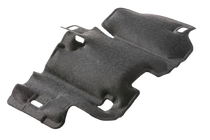
Engine Encapsulation
Further possible composites can be used for door trims or package trays, for example. With the best suitable combination of natural fibers and Acrodur®, tailor-made solutions can be created to achieve your desired properties for a certain composite with an average renewable content of 75 %.
With the Biomass Balance Approach, fossil materials can even be replaced by renewable sources up to 100 %.
Service and Technical Capabilities
Our pilot plant offers the possibility to conduct a broad spectrum of trials and material tests with small input amounts of raw materials. A team of experts with state-of-the art equipment is here to support you in finding solutions for your questions and issues, ready to give you advice based on their long-term experience.
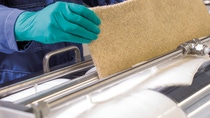
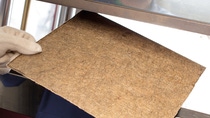
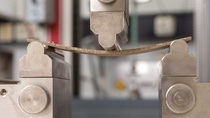
Preparation of prepregs
No matter whether you are using foam, bath or spray impregnation, we can choose from a wide range of application techniques.
Molding
With our presses, we can conduct both thermoplastic and duroplastic molding of composites. While planar sheets are beneficial for mechanical testing, the installation of different model molds makes it possible to generate shapes simulating warpage and stress in real processing.
Testing
In our testing labs, we are able not only to characterize samples with respect to mechanical parameters such as bending stiffness, Young’s modulus or impact resistance, but also to analyze specific parameters like odor, FOG, VOC, total organic carbon, etc.
Discover

BASF is investing in its dispersion production sites to meet growing customer demand in EMEA

Technical Information: Preservation of Polymer Dispersions
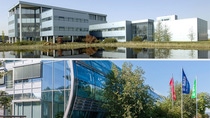
Meeting the growing demand: BASF production sites in Heerenveen and Trostberg receive biomass balance certifications
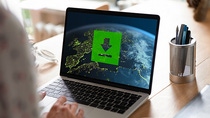
Access your PCF data online
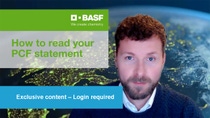
How to read your PCF statement
Contact us
Not found what you were looking for? Reach out to us for assistance.
Subscribe to our News-Service
Don’t miss the latest news on web seminars, sustainability, regulatory and product innovations.