MyIndustryWorld
Prof. Dr. Thomas Schiele: "Sustainability is in our DNA"
Sustainable chemistry needs to factor in a substance’s entire lifecycle. This requires close cooperation between all the players involved.
Prof. Dr. Thomas Schiele, Vice President Adhesives, Fiberbonding & Paper Coating Chemicals, explains in the following interview why his business unit is a pioneer of and driving force behind more sustainable solutions.
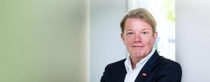
Many people regard sustainability and chemistry as being contradictory. Why is that?
Many people still visualize the images of environmental disasters that occurred during the last century. Think of the Seveso or Sandoz accidents. But the image of the chemical industry has been improving since the 1990s; it has learned from the past. Sustainability has been an integral part of our strategy for almost 25 years. We wish to drive sustainability forward. That is why our motto is “We create chemistry for a sustainable future.”
How sustainable is BASF’s Adhesives business unit?
Sustainability is part of our DNA. We help our customers to make their products more environmentally compatible. We achieve this, for example, by applying our biomass balance approach. You can compare the principle involved with purchasing electricity: either the supplier uses conventional sources to generate electricity or you buy green electricity. Similarly, you can order dispersions from us for which we use fossil feedstock or renewable raw materials, such as biogas, at the very first steps of chemical production in our plants. Taking this option helps to conserve resources and reduce greenhouse gas emissions. To put it in concrete terms: customers can, for example, save 500 kg of emissions per tonne of our Luphen MB 3695 product compared with a standard product. The next objective is production of purely bio-based adhesive raw materials – we are already working on that.
Our products themselves are also sustainable. For example, our adhesive raw material acResin®, a UV-curable 100% acrylate for the production of specialty pressure-sensitive adhesives. It provides an alternative to solvent-based adhesives and, helps our customers at the same time to reduce CO2 emissions. We also developed water-based raw materials for adhesive solutions already twenty years ago, but there was no market for them back then. Adhesives manufacturers were skeptical about whether water-based dispersions could be used to achieve equally effective adhesive properties as solvent-based raw materials. That took some persuasion. We now supply a wide range of industries with sustainable, solvent-free basic and specialty chemicals for bonding applications.
What application examples do you have in mind?
Worth mentioning are our water-based polyurethane dispersions, which are ideal for the technical lamination of products from a wide range of different industries, like applications in the furniture, footwear and automotive industries. We not only offer adhesive systems that are solvent-free, we also have fully biodegradable solutions.
“Taking an integrated view is always required for sustainability to succeed.”
However, these are just two of the many other aspects of sustainability. We take a broader view of this issue, and have defined a series of criteria that all contribute to sustainability and that we have set as the benchmark of our product philosophy.
What criteria are you alluding to?
I am thinking, for example, of the CO2 footprint or Product Carbon Footprint (PCF), which we ascertain for all our products. This value reflects all the greenhouse gas emissions caused by a product during the various phases of its lifecycle. We are doing all we can to keep on reducing this footprint for our products.
Another key criterion for a sustainable product is its recyclability. The best example of this is our water-based laminating adhesive system, Epotal. It is free of aromatic isocyanates, free of glymo and any organic solvents. That is why it is ideal for laminating flexible food packaging. A smart end-of-life solution makes this packaging fully recyclable.
What form could such an “end-of-life” solution take?
The adhesive raw materials are designed on the one hand to hold or bond the packaging layers – for instance the films that make up a chips bag – securely together. On the other hand, they are intended to release or debond these layers when they are recycled. The bonded films must therefore be capable of being easily separated again from one another, to enable them to be returned as homogenous materials to specific flows of recyclables during the course of the recycling process. In this context, this is referred to by experts as “debonding on demand”. That means that the adhesive should bond as effectively as possible when required, but should also be removable when the packaging has served its purpose.
That sounds complex. Why not limit yourself from the outset to single-layer packaging?
That’s no longer an option, due to the high demands placed on packaging nowadays. On the one hand, packaging needs to be food-grade and must not allow foreign substances to migrate into the food. While on the other hand, it needs to form a secure oxygen barrier and keep the food fresh for as long as possible. A single film is not capable of that. That is why packaging nowadays needs to be manufactured smartly and also be recyclable. However, that does not just apply to packaging, but to products of all kinds consisting of multiple components that are bonded together.
What does that actually entail in terms of your product development work?
We already have to think end of life when developing basic materials, i.e., at the start of the product lifecycle. What’s the point of processing the most ingenious raw material into an absolutely fantastic adhesive, if, at the end of the material cycle, it is not capable of being cleanly separated or at worst even contains undesirable environmental pollutants?
“We help our customers to make their products more environmentally compatible.”
Conversely, that means for us that truly sustainable solutions can only be actioned together with all the players involved in the process – with us as the manufacturer of the basic and specialty chemicals, with the adhesive manufacturers, the product and packaging manufacturers, the brand owners as well as with the recycling industry.
That sounds good. But in practice doesn’t it take a very long time to replace plastic packaging, for example, with smart solutions? Given the urgency, this needs to happen more quickly, doesn’t it?
It is true that all industries are desperately seeking sustainable solutions. But such solutions cannot be developed in the space of just a few weeks or even months, because major technological advances would then be required to some extent within a very short space of time. If a glass or plastic bottle is to be replaced by a paper bottle, that represents a paradigm shift, a completely new way of thinking. Not only do new adhesive solutions need to be found, but new machines, new application technologies, new timing systems etc. are also required on the processing side. Things that have never been questioned for decades are to be changed all of a sudden. Such a switch, like from plastic to paper, is certainly feasible, but doesn’t happen overnight.
How are you approaching this challenge?
We are working on solutions together with our partners. For example, we are currently developing dispersions for paper packaging and equipping them with the appropriate barrier technologies to extend the shelf life of food. Such innovations represent small but important steps in the right direction.
Taking an integrated view is always required for sustainability to succeed on a large scale. The fact that substances do not release pollutants into the environment and are biodegradable is an important piece of the jigsaw. But that alone is not sufficient to enable us to achieve our major objective, namely for the BASF Group to become climate-neutral by 2050 – in other words, ceasing to emit CO2. This means that we will also factor power generation into our calculations and continue to reduce our use of fossil fuels.
Related topics
Contact us
Not found what you were looking for? Reach out to us for assistance.
Subscribe to our News-Service
Don’t miss the latest news on web seminars, sustainability, regulatory and product innovations.