MyIndustryWorld
acForm® - Groundbreaking binder technology for curved and deeply structured wood fiberboards
The new BASF resin acForm® represents the first dispersion-based binder worldwide for the blowline process and enables the production of 3D moldable wood fiberboards (3MF). These boards are perfectly suited for shaping and embossing technologies, adding a new dimension to the furniture and interior design industry.
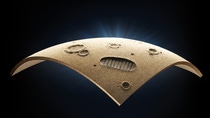
Benefits of acForm® technology
- Time- and cost-efficient process
- New design options & high surface quality for 3D wood fiber parts
- High degree of wood utilization
- Non-added formaldehyde and storage-stable binder technology
A small step for you
A giant leap for your customer
BASF’s acForm® enables the production of a new wood-based material for the furniture industry. Specifically, it enables the production of a thermoplastic composite, which is storage-stable and suitable for production on existing fiberboard production lines.
In contrast to standard thermoset boards, this new wood-based material enables a post-moldability and surface structuring of the composites. This can be achieved in short cycle times by using standard furniture molders’ equipment. The increased moldability of the composite enables new design options.
The 3D moldable fiberboards (3MF) can be processed into traditionally molded parts such as seat shells, seat backings, and other curved or deeply structured components. As formaldehyde is not added to the binder system, the working environment is further improved.
BASF offers the possibility of producing acForm® based on the biomass balance approach, using 100 % bio-based raw material.
Shaping wood composites with acForm®
BASF’s binder technology for new designs, with efficient production on standard equipment.
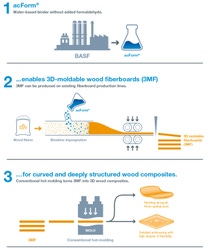
3MF benefits for molders and OEMs
- consistent quality and storage storability of prepreg (flat board)
- short molding cycle times
- new design options for surface and shape
- superior surface quality of molded (compressed) parts compared to those produced by CNC milling
- improved properties for standard finishing technologies such as lacquering or powder coating
- safe working atmosphere through non-added formaldehyde
- high degree of wood utilization and scrap reduction
- recyclability as used wood
acForm® benefits for board producers
- processability on existing blow line equipment
- high productivity of board production
- water-based dispersion with low VOC
- excellent storage stability
- safe working atmosphere through non-added formaldehyde
- compatibility with additives (e.g., water repellents, pigments, flame retardants)
Learn more about acForm® and connect with our expert!

Discover
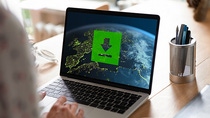
Access your PCF data online
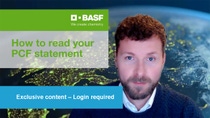
How to read your PCF statement
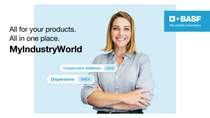
Discover „MyIndustryWorld“ - the new service portal of BASF
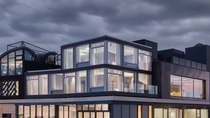
Upcycling solutions for interior design at NEST
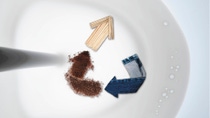
Fiber Bonding for Upcycling
Contact us
Not found what you were looking for? Reach out to us for assistance.
Subscribe to our News-Service
Don’t miss the latest news on web seminars, sustainability, regulatory and product innovations.